
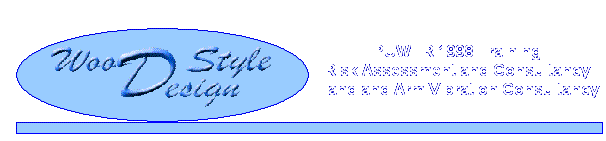
The new regulations are Control of Vibration at Work act Regulations 2005.
The new regulations impose strict new limits on the length of time employers can expose workers to vibration and employers will be liable to criminal prosecution if the regulations are ignored.
The HSE have estimated that 5 million people use vibrating machinery and 2 million are at risk of injury. It is estimated that 44% of companies will be over the new limit.
You could use manufacturers data to access the risk but this is based on static bench tests with no work load, considering this data can be 400%-500% inaccurate compared to the same tool being used under varying conditions. Therefor the only reliable method is to have each machine tested and labeled.
It is a misconception by some managers to assume because their staff use these tools infrequently they are outside the scope of the new regs . If you do not test the machines how would you know if they were above the new upper limit !
By Law Employers Must
Provide training on health risks and the safe use of equipment. Assess the risk of the health of employees and plan for its control. Manage the risk by measuring the vibration on all you’re machines. Provide suitable equipment. Maintain equipment. Provide health surveillance for you’re employees where risks cannot be completely eliminated. Provide reports to the relevant authorities of cases of HAVS. Consult with you’re H & S representative on your proposal to deal with vibration.
What’s included in the price ? Staff awareness training. how to avoid HAVS, medical conditions, Measuring the machines for vibration, and labelling them Using tools correctly. Discuss with management, reducing and controlling the risk, Providing the relevant forms and software.
The staff training would cover 6 main elements. 1/ Describe and discuss the medical condition and assess the groups at risk. 2/ The best ways of avoiding HAVS the correct clothing, gloves, and the correct way to hold and operate machinery. 3/ Which workers are at risk. 4/ Which tools are at risk. 5/ Purchasing new tools. 6/ The regulations and how they effect you. On completion the staff would receive a certificate of attendance.
How the machines would be tested. I would use a class 1 human vibration meter connected to a triaxle accelerometer. The accelerometer is fixed to the handle of the machine. The meter is switched on for a measured time and the X Y Z readings are then transferred onto computer software, that gives a vibration reading and daily dose. This information would be typed on to a label and fitted to the machine.
I am an accredited City & Guilds training consultant. I provide training for prisons. blue chip companies and local councils. I am currently providing training for more than 200 hundred hospitals plus universities and colleges.
Mel Vaughan, Woodstyle Design, 42 Bawtry Rd, Harworth, Doncaster DN118NX
Tel : 0870 300 3999 Mobile 07748790775
Email : [email protected]